Construction Workers Suffer Falls and Other Injuries at Rates far Surpassing Most Other Professions
Construction workers suffer falls and other injuries at rates far surpassing most other professions. To prevent injuries and fatalities, construction companies must create a culture of safety at their work sites, keeping safe practices at the forefront of workers’ minds as they go about their work.
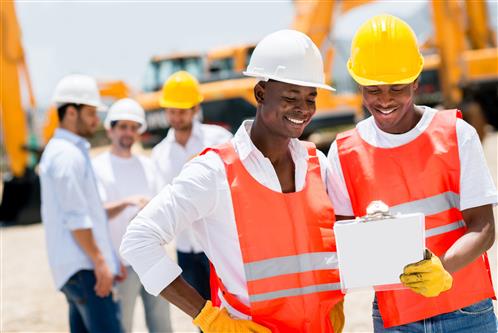
About one in five worker deaths occur in the construction industry each year. It’s little surprise, as construction workers face a number of dangers in their profession, such as falls from high places, getting hit with materials that fall from heights, working with sharp objects, working with electricity, etc. The four most common causes of fatal injuries among construction workers are:
- Falls
- Electrocutions
- Getting struck by falling objects
- Getting caught between objects
Worker injuries and fatalities can greatly impact construction companies, resulting in terrible human costs as well financial ones such as fines, health care expenses, and litigation. Finding ways to improve human safety will help construction managers avoid tragic circumstances and financial disaster.
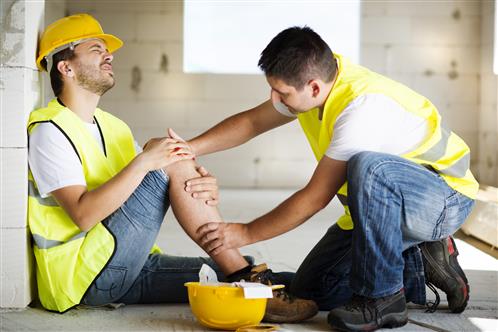
Some common safety practices construction managers should implement onsite include:
- Stringent fall avoidance policies – Falls are a huge contributor to worker injury, so lots of training on proper practices is needed. Workers should be trained on safe weight limits for equipment. They should also learn how to properly inspect and set up ladders, mast lifts, and scaffolds. Emphasis on using fall avoidance equipment like rails and harnesses is also necessary.
- Avoidance of electrical shocks – Train employees to make sure electricity is turned off before working on wiring or electrical components. Also teach workers to avoid risky shortcuts such as using home extension cords, removing the third prong from a plug or overloading power boxes. Training on proper safety gear is also essential.
- Avoidance of air hazards – All employees need training on how to avoid risks posed by toxic fumes and pollutants. Employees should learn to follow safety instructions when handling lacquers, paints, varnishes, and other compounds that can cause respiratory harm. Employees also need to learn when to use safety equipment such as protective masks.
- Avoidance of falling objects – Enact strict policies regarding the proper storage of tools and materials, particularly when employees are working on surfaces where items can fall and strike people below. Be sure to require employees to wear hardhats on these sites.
- Practice of ergonomics – While this area of safety deals more with comfort than preventing fatalities, good ergonomic practices can save companies in work-related injuries and productivity losses. Using balanced, comfortable tools will prevent injuries and allow employees to work for extended periods without pain or discomfort. Proper lifting practices can help workers avoid back injuries, which can carry high health costs and send absentee rates spiraling. Providing stools and benches for workers can also help reduce knee and back injury.
Founded in 1932, Prudential Overall Supply is an established name in the uniform and safety apparel business, and it has a reputation for high quality products, including men’s work clothing, flame resistant uniforms, and more. To learn more, contact us at 800-767-5536.