Creating a Safer Work Environment in Your Industrial Facility
Worker safety is one of the most important considerations in any industrial facility. A healthy, injury-free workforce is essential to the smooth operation of any business. Whether you operate a warehouse, a food manufacturing facility, or an auto parts manufacturing plant, there are steps operations managers can and should take to ensure worker safety. Read on to learn more.
Ensure employees are wearing appropriate clothing and safety gear at all times.
Workwear that is functional and which has protective features such as built-in flame resistance can reduce accidents and injuries. Safety gear such as high-visibility clothing, hard hats, eye protection, and gloves are essential in many industries. Coveralls are necessary to protect workers’ skin in many industries, from automotive to chemical manufacturing. Make sure your workers have all the protective gear and tools they need to stay safe on the job.
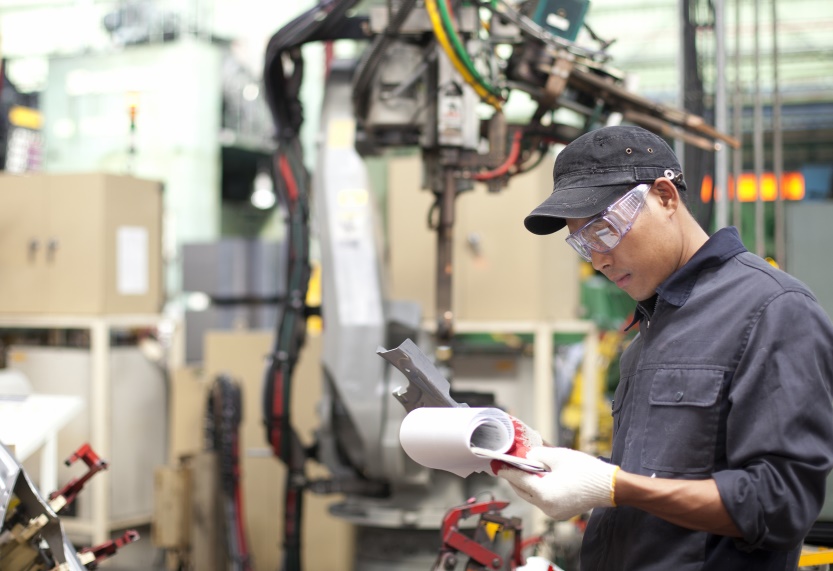
Conduct employee safety training meetings regularly.
In addition to those required by law, your company likely has its own worker safety rules and regulations to maximize worker safety. It’s important to conduct safety meetings at regular intervals for existing employees. New employees should always receive safety training as part of their orientation or new hire training program. To make these meetings more enjoyable and interesting, avoid simply reading rules from a safety manual. Instead, consider creating a media presentation that is visually interesting, and promote interactive participation from employees. Where possible, incorporate games or even role playing scenarios that get employees even more involved. Combining different mediums, such as pictures, DVDs, games, and role playing will help employees retain the information. Test workers’ knowledge at the end of each training session.
Create a safety committee.
A workplace safety committee with active involvement by both employers and employees can help strengthen existing safety measures within your industrial operation. To establish a safety committee, you’ll need to determine the resources at your disposal, map out objectives and goals for the committee, and establish the roles and responsibilities of the different committee members. Next, you’ll need to assemble a team, which may include supervisors, employees, volunteers, safety specialists, and health specialists. Next, conduct a workplace analysis to identify and eliminate potential hazards, and finally, design and implement the safety training and education program. You may consider offering some kind of incentive for those who choose to participate and stay actively engaged in the committee.
Ensure safety rules and guidelines are placed in a highly visible and accessible area.
Safety rules and information are of little use if they are not placed in common areas that all employees have access to. The more safety signs posted, the better.
Perform regular maintenance and safety checks on machinery.
Malfunctioning or poorly-performing equipment can not only slow down production, it can also present safety hazards to your workers. Don’t wait until a machine is making funny sounds, giving off strange smells, or otherwise not functioning properly, which can lead to more costly problems and increase the risk of injuries. Have equipment inspected as often as is recommended by the equipment manufacturer, if not more frequently.
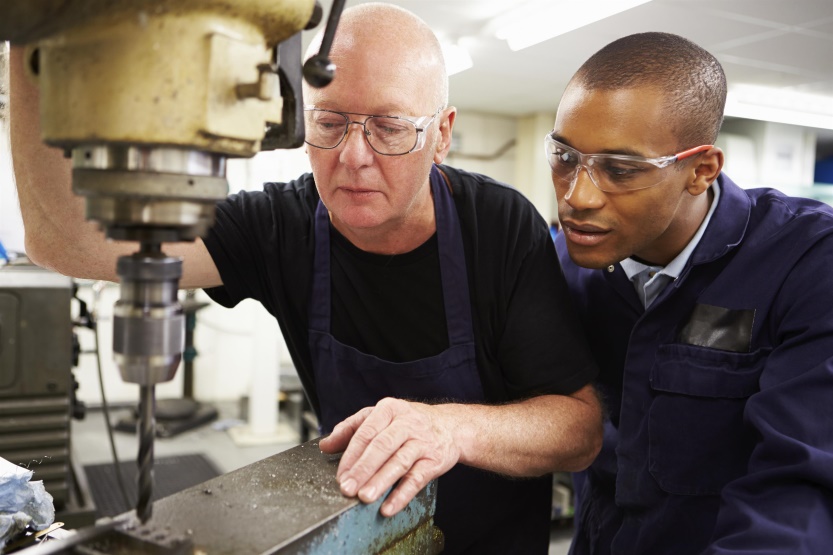
Ensure proper lighting and ventilation.
Proper ventilation in industrial workspaces is vital for:
- Maintaining an adequate oxygen supply
- Flushing hazardous concentrations of toxic particles and gases from the air
- Reducing or eliminating foul odors
- Controlling air temperature and humidity levels
Properly functioning carbon monoxide and other monitors (depending on your industry) should also be installed throughout the facility.
Proper lighting is essential for:
- Adequately lighting equipment and workspaces
- Illuminating trip hazards on the ground
- Preventing errors and accidents
- Eliminating shadows that can hide sharp edges, spills, trip hazards, etc.
Make sure your ventilation and lighting systems are adequate for your facility. One of the easiest ways to make an initial assessment of whether your facility has sufficient lighting is to make visual inspection of the facility yourself and ask employees about their experience. If they report straining to see objects, or they report dimly lit areas that make it difficult to operate equipment, this should prompt you to bring in a lighting expert to address the situation.
Train employees on proper lifting techniques
In virtually any industrial workplace, some amount of lifting is going to be required. Proper lifting techniques should be incorporated into your safety training program. Musculoskeletal disorders, including back injuries, accounted for 380,600 of all the days-away-from-work cases in 2013, according to the Bureau of Labor Statistics. That accounted for one-third of all such lost work days.1
Proper lifting technique involves:
- Keeping feet shoulder width apart
- Squatting down, bent at the hips and knees
- Slowly lifting, keeping back straight, and straightening at the hips and knees only
- Holding the load as close to the body as possible
- Avoiding twisting the body, using only the feet instead to change directions
- When setting load back down, bend knees and hips only, keeping back straight
Workers whose jobs require lifting and moving moderate to heavy loads should be provided with the appropriate back support equipment, such as removable back support braces, to help prevent injuries.
Ensure workers’ uniforms are kept clean.
Uniforms and/or protective clothing that become soiled during the course of work are not only unsanitary, but can be hazardous to employees. Stains from oil, grease, and other chemicals can be inhaled, absorbed through the skin, or accidentally ingested, and can also present a fire hazard. Relying on employees to properly launder their work uniforms is risky.
This is why many industrial facilities opt for a uniform rental or leasing service that also provides laundering. A survey conducted by TRSA titled the “National Consumer Survey and Business to Business Survey of Uniform and Textile Rental Decision Makers” found that 54% of industrial business decision-makers reported renting uniforms for their workers.2 Eighty percent of those surveyed said renting industrial uniforms saved their company time and money, and improved the appearance of employees.
A service that drops off freshly laundered workwear and picks up soiled uniforms can improve worker comfort and safety, and your bottom line.
Sources:
To learn more about fostering a safer work environment with industrial protective gear, visit https://www.prudentialuniforms.com/services/uniforms-and-apparel/industrial-shirts/