Cleanroom Contamination: Causes, Prevention, and Essential Cleaning Tips
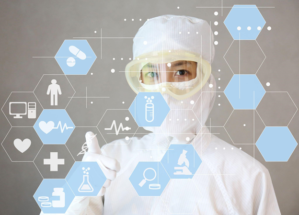
Maintaining a contamination-free cleanroom is critical to industries like biotechnology, pharmaceuticals, and electronics manufacturing. Any breach in contamination control can result in compromised experiments, defective products, or even safety hazards.
Cleanrooms are designed to minimize airborne particles, microbes, and other pollutants, but that goal is only achieved with constant attention to process, behavior, and the smallest details. What may seem insignificant in another setting—like a forgotten pen or a poorly fitted garment—can become a serious contamination risk inside a cleanroom.
If your company operates a cleanroom, you already know the level of control required to keep it compliant. Understanding the most common causes of contamination, how to prevent them, and how to clean correctly is essential to preserving the integrity of controlled environments.
Understanding Cleanroom Environments
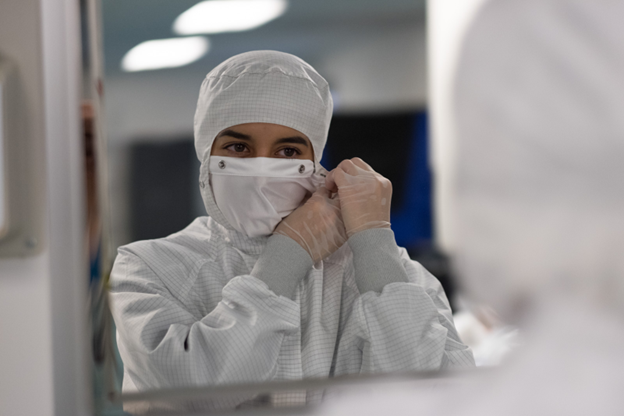
Cleanrooms adhere to specific classifications outlined by ISO standards, emphasizing the necessity of stringent cleanliness and sterility. These controlled environments demand rigorous management of both particulate and microbial contaminants to uphold the integrity of delicate processes and products.
The classification system delineates various levels of cleanliness, with each designation reflecting stringent criteria for airborne particle concentration and microbial presence. For instance, the requirements of an ISO 3 cleanroom are more strict than those of an ISO 7 facility. Nonetheless, the same broad purification principles tend to apply to all cleanrooms.
Achieving and sustaining these standards requires precise monitoring and control of factors such as air filtration, personnel attire, and surface disinfection protocols. Ultimately, the meticulous management of cleanroom conditions ensures the reliability and quality of the manufactured goods or processes within these specialized environments.
Common Causes of Cleanroom Contamination
Cleanrooms are vital for industries that process extremely delicate materials that can be compromised by airborne particles. Vaccines and microelectronics are only two types of products that benefit from the sterile environment of a well-managed cleanroom. However, keeping airborne contaminants below an acceptable threshold is always easier said than done.
In the tightly controlled environment of a cleanroom, contaminants can arise from a wide variety of sources—including some that are easily overlooked by people who are not accustomed to the stringent maintenance demands of these areas. Understanding where contaminants come from is key to controlling them properly.
1. Personnel
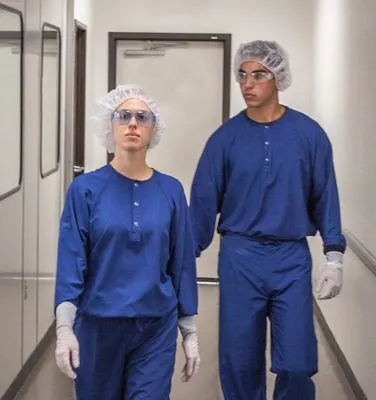
By far the most common source of contamination in a cleanroom is the human personnel inside it. In fact, human beings account for over 80% of the contaminants found in these areas.1 Much of this contamination happens without any effort on our part, as we typically shed about one billion skin cells every day.2
When we’re in motion—e.g., walking from one place to another, or simply gesturing with our hands—the rate of shedding increases exponentially. Talking also expels a substantial amount of potentially harmful particles into the air.
Other contaminants people can bring into a cleanroom are germs, bacteria, viruses, and bodily fluids and oils. If an employee is ill, their contamination risk skyrockets. Shedding skin disorders such as dandruff, eczema, and psoriasis are particularly troublesome for cleanrooms.
Cosmetics, deodorants, perfumes, and lotions also contribute significantly to the presence of particles in the air. For that reason, technicians are usually discouraged from using products of this nature if these workers are to be inside a cleanroom for any length of time.
Another big cause of cleanroom contamination is the clothing worn by personnel. Fabrics that are prone to linting create a hazard in these highly sensitive environments.
2. Cleaning Products
It goes without saying that a cleanroom should be kept clean. However, the process of ridding the area of dirt and other contaminants can easily introduce other pollutants into the environment. Actually, this is a major source of contamination in a clean room.
All cleaning products should be approved for use in cleanrooms; normal consumer accessories aren’t suitable for the purpose. This means using mops and cleaning wipes with non-particulating properties. Liquid solvents need to be cleanroom-friendly as well—they should not leave behind residues that might contaminate the area.
3. Office Accessories
Cleanroom technicians are often tempted to bring their own pencils or pens into the area. The problem with this practice is that these seemingly harmless objects can introduce bacteria into the cleanroom.
For example, marker pens sometimes harbor molds, which can spread into the air. That’s why many cleanrooms mandate the use of electronic recording devices that never leave the facility.
4. Processing Equipment
The kinds of equipment used to aid in the processing of cleanroom products can contribute to the amount of contaminants in the air. Some generate gasses or expel other types of particles that can cause contamination. Furthermore, equipment that vibrates during use tends to throw particles into the air.
These are all considerations that should be kept in mind before bringing a particular piece of machinery into the cleanroom.
5. Static Electricity
This is an especially dangerous hazard for cleanrooms that process sensitive electronics. Flooring, wall panels, furniture, work surfaces, and clothing are all capable of generating static that can harm delicate electronic parts. In some cleanrooms, a sudden spark can even trigger a potentially deadly fire or explosion.
6. Airflow and HVAC Systems
From vibrations between objects to air cooling and heating systems, particles are going to get in, and they need to be removed through the appropriate cleaning processes. Cleaning procedures have to be clearly defined and specific protocols followed in order to avoid contaminating the cleanroom.
7. Lack of Preventative Maintenance
Maintenance is another essential aspect to lowering the likelihood of causing contamination within a cleanroom. Any systems used to keep particles out should be inspected on a regular basis. Not establishing maintenance schedules and adhering to them will definitely increase the possibility the cleanroom is going to be contaminated.
Additionally, someone has to be tasked with measuring particle levels within the cleanroom frequently, so that their levels can be monitored.
How to Keep a Cleanroom Contaminant-Free
Not all cleanrooms have identical requirements when it comes to minimizing contamination. Regardless of classification, however, effective cleanroom contamination control relies on strict personal habits, proper cleaning procedures, and the right tools.
1. Provide Proper PPE (Personal Protective Equipment) and Cleanroom Garments
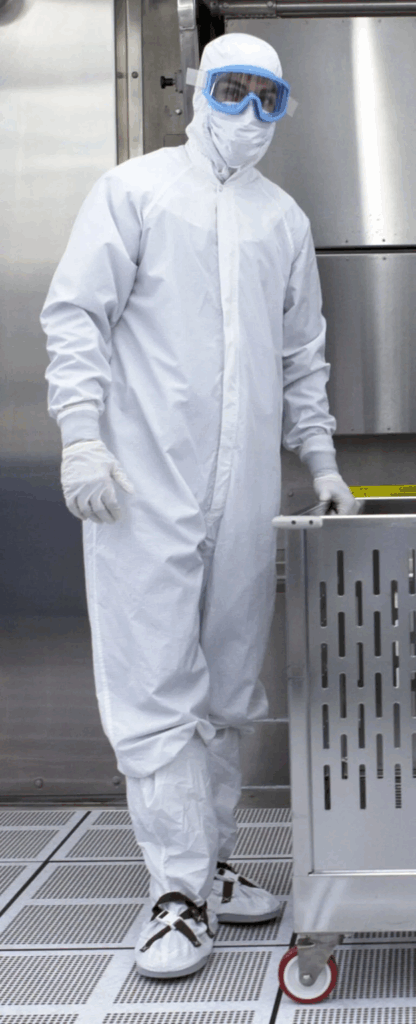
Personnel entering cleanrooms are required to adhere to specific dress codes and safety requirements, including wearing appropriate PPE and specialized cleanroom garments.
These may include:
- Coveralls
- Lab coats
- Face masks
- Goggles
- Shoe covers (“booties”)
- Hairnets
- Bouffant caps
- Gloves
Cleanroom garments are essential for maintaining barrier control and reducing shedding of skin and hair. Employees must also shower prior to entry and avoid lotions, deodorants, and cosmetics that could introduce particles. Make sure all employees thoroughly wash their hands with soap and water before putting on apparel and PPE.
2. Teach Proper Gowning Procedures
Personnel should be aware of the correct way to don uniforms in order to avoid contaminating the fabric. They should also have access to a dedicated dressing room. Training should include step-by-step cleanroom gowning procedures, visual walkthroughs, and guidelines for what to do if a mistake is made. Regular audits of cleanroom gowning compliance help reinforce these protocols.
3. Make Sure PPE and Apparel Are Removed Correctly and Carefully
When leaving a cleanroom, make sure to promptly remove the PPE using a top-down approach. Any potential contaminants tend to be pulled down by gravity.
For reusable garments, place them carefully into the soiled bag while still having your gloves on. Remove protective gloves last by turning them inside out and disposing of them in the proper waste bin. Now wash your hands with soap and water.
Proper exit procedures help prevent cross-contamination. Train employees to follow a consistent routine and enforce those steps at every shift.
4. Install HEPA or ULPA Filters
HEPA (high efficiency particulate air) filters remove 99.97% of airborne particles in your cleanroom, while ULPA (ultra low particulate air) filters extract 99.999% of particles. Both types can severely cut down the concentration of particulate matter circulating through your facility.
Schedule regular replacement and monitoring intervals to maintain air purity and meet ISO compliance levels.
5. Clean and Disinfect Frequently
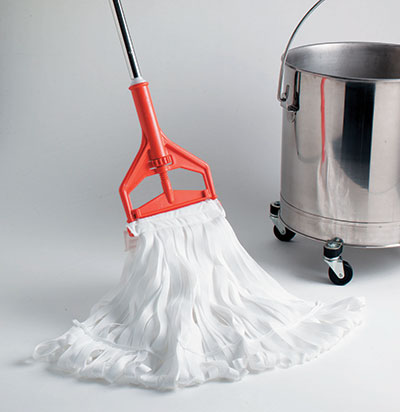
The cleanroom also needs to be cleaned and disinfected to reduce the risks of contamination. There are different types of cleanroom supplies that can be used for cleaning and disinfecting. Make sure to be careful when taking cleaning items in and out of the clean room to limit potential contamination.
Daily discipline in cleaning protocols is non-negotiable. Surfaces, tools, and air must be monitored and cleaned on a defined schedule.
Essential cleanroom cleaning supplies include:
- Particle-free wipes
- Cleanroom-compatible disinfectants
- Cleanroom vacuums
- Non-shedding mops and wipes
Document cleaning frequencies and inspection checklists. Replace air filters regularly and monitor airflow patterns and pressure balances.
6. Use Only Cleanroom-Designated Items
You should have specific cleaning products, equipment, and other such items that are just used in the cleanroom. For example, with reusable cleanroom mops, you would want to employ proper mopping techniques. Certain mops are designed for ceilings, walls, and floor cleaning to meet the specific cleanroom cleaning requirements.
Never bring tools or materials into the cleanroom that have been used elsewhere. All cleaning equipment should be labeled and restricted for cleanroom use only.
7. Install Anti-Static and Static-Dissipative Materials
Ensuring that your floor panels, furniture, work stations, etc., are made from these kinds of materials will lower the risk posed by static electricity. Floors, benches, and walls made with static-dissipative materials reduce the movement of airborne particles and protect sensitive electronics from ESD damage.
8. Enforce and Train on Entry and Exit Protocols
The most common way contamination occurs is from employees who are not trained correctly. They could bring in a dirty piece of equipment or cleaning item that was used elsewhere. They could remove their face mask while in the cleanroom because their nose itches.
Take the time to go over your cleanroom cleaning protocols, including the contamination precautions at entry and exit points, when taking cleaning products in and out of the cleanroom.
Set clear rules about what can enter the cleanroom and make sure all materials are inspected or sterilized first. Gowning areas should have proper airflow and signage. Train staff regularly on entry procedures and update protocols when equipment or practices change.
9. Practice Proper Hygiene and Health Screening
Proper hygiene goes beyond washing your hands frequently and wearing PPE. It also includes ensuring that your employees bathe daily and do not wear any jewelry, makeup, cologne, cosmetics, skin creams, antiperspirants, or other such things that could cause contamination.
Sick employees or those with skin conditions (like eczema or dandruff) should not be permitted to enter, as these are common sources of microbial contamination in cleanrooms. Consider health screening policies that include temperature checks and sick-day accountability.
10. Use Environmental Monitoring Systems
Real-time monitoring tools help detect airborne particulates, pressure imbalances, and microbial risks before they reach critical levels. Integrating these systems into your daily operations gives you constant visibility into cleanroom conditions.
Use sensors and tracking systems to:
- Monitor air quality and humidity
- Alert staff when thresholds are exceeded
- Ensure consistent compliance with ISO standards
- Provide automated logs for audits or inspections
11. Use High-Quality Cleanroom Uniforms
This may be the number-one strategy for keeping your cleanroom safe. Renting or purchasing cleanroom uniforms from a trusted third-party supplier can go a long way toward reducing pollutants in your facility.
Made of breathable, non-linting, ESD materials, cleanroom uniforms sharply reduce the amount of bodily contaminants released into the air and the hazards generated by clothing.
Responding to Contamination Incidents

Even with rigorous protocols, contamination can still occur. Whether caused by human error, equipment failure, or an unforeseen breach, what happens next is critical. A clear, documented response plan helps minimize disruption, protect sensitive products, and prevent recurrence.
Here’s an example of a well-structured contamination response plan:
- Stop Operations Immediately
Cease all activity in the affected area to prevent the spread of contaminants. If needed, isolate adjacent zones to contain potential cross-contamination.
- Notify Key Personnel
Alert the cleanroom manager, quality control team, safety officers, and any other designated staff. Quick communication ensures a coordinated and documented response.
- Secure and Quarantine Affected Materials
Identify any exposed products, equipment, or supplies. Move them to a secured holding area or seal them in designated containment units for further inspection or disposal.
- Identify the Source of Contamination
Conduct a root cause analysis. Review recent maintenance, supply deliveries, staff movements, and environmental monitoring reports to trace the issue.
- Clean and Re-Sanitize
Use approved cleanroom cleaning supplies to disinfect affected surfaces, tools, and pathways. Replace filters if needed, and ensure the room is re-validated before resuming work.
- Log and Report the Incident
Document the time, location, suspected cause, team response, and any affected materials. Detailed logging supports traceability and regulatory compliance.
- Review and Update Procedures
Evaluate what failed. Was it a lapse in training, equipment defect, or missed protocol? Use findings to strengthen SOPs, retrain staff, or improve preventative systems.
Cleanroom teams should rehearse contamination scenarios as part of their ongoing training program. Being prepared not only limits potential damage but reinforces a culture of accountability and contamination control.
The Role of Cleanroom Maintenance
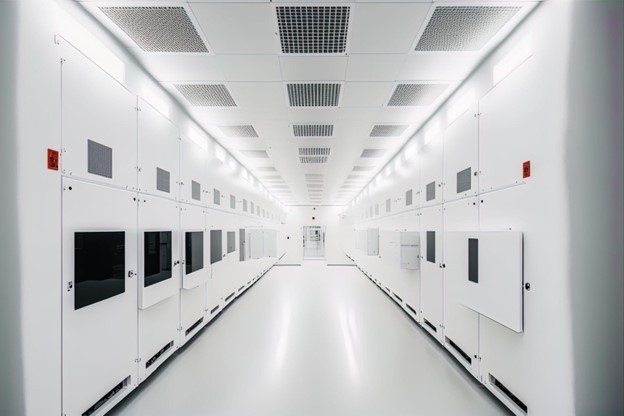
Routine maintenance is essential to keeping cleanroom systems working properly. It helps ensure filters, airflow equipment, gowning stations, and other critical infrastructure perform as intended. Without it, even the best contamination control plan can fail.
Any systems used to keep particles out should be inspected on a regular basis. Not establishing maintenance schedules and adhering to them will definitely increase the possibility the cleanroom is going to be contaminated. Additionally, someone has to be tasked with measuring particle levels within the cleanroom frequently, so that their levels can be monitored.
Particle counts should be logged and reviewed routinely. Schedule-based servicing of HVAC, filtration, and equipment systems helps prevent contamination risks before they reach critical levels.
Preventing Cross-Contamination During Repairs
When maintenance technicians need to enter the cleanroom, any repairs or upgrades inside the controlled environment can create contamination if not properly planned. Anytime technicians enter to service machinery, strict controls should be in place.
Common cross-contamination prevention measures include:
- Isolating the work area with cleanroom-safe barriers
- Only allowing the use of tools cleaned and sealed before entry
- Scheduling repairs during low-risk periods (off-hours or production lulls)
- Supervising maintenance teams to ensure procedures are followed
Choosing the Right Cleanroom Supplies
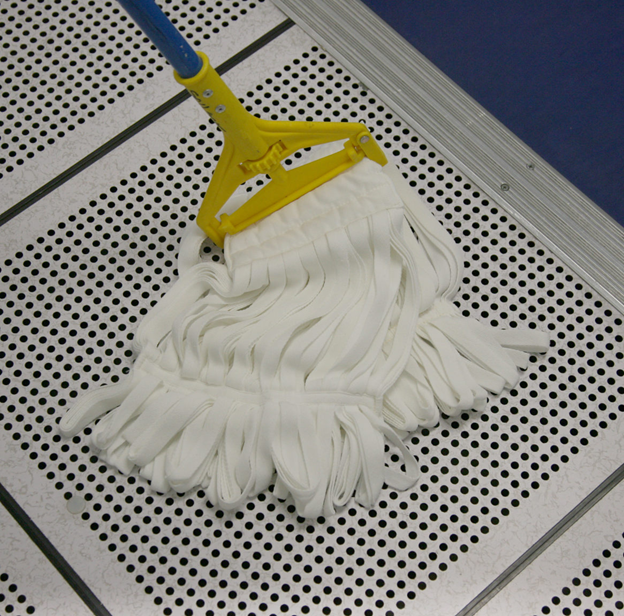
Cleanroom success doesn’t depend on uniforms alone. Cleaning supplies, tools, and accessories play an equally critical role in contamination control. From floor mops to goggles, the materials used every day inside the controlled environment must be chosen carefully and sourced from trusted providers.
Here’s what to look for when selecting cleanroom supplies:
- Products that are tested and rated for ISO or GMP environments
- Non-shedding, low-residue materials designed for cleanroom compatibility
- Packaging that prevents contamination before use
- Instructions for use, storage, and sterilization
- Traceability and batch documentation for quality assurance
Supplies should not be shared between cleanroom and non-cleanroom areas. This includes gloves, mop heads, waste bins, and safety goggles. Everything should be cleaned or laundered in a controlled setting or safely disposed of after use.
In addition to garments, Prudential Cleanroom Services, a division of Prudential Overall Supply provides reusable non-garment cleanroom supplies, including mops and goggles specifically engineered for regulated environments. These products are designed to maintain integrity across multiple uses, offering both cost-efficiency and compliance when supported by proper laundering and handling protocols.
Partnering with a provider of cleanroom contamination solutions like Prudential ensures not only high-quality supplies but also the process support and delivery reliability required to keep your operations clean and compliant at all times.
Selecting and Maintaining Cleanroom Uniforms
Cleanroom uniforms play a critical role in keeping particulate and microbial contamination under control. Choosing the right garments—and managing them properly—helps maintain your cleanroom’s compliance and performance.
What to Consider When Selecting Cleanroom Clothing
When choosing cleanroom garments, it’s important to balance protection with practicality. The right materials and design ensure safety without sacrificing comfort or mobility.
When considering cleanroom apparel:
- Material must be compatible with cleanroom processes
- Garments should provide effective static control
- Choose options that are durable under frequent laundering
- Ensure design allows sufficient range of motion
- Select clothing that minimizes particle generation
Maintaining Cleanroom Uniforms
Even the best garments can fail if not handled properly. Ongoing inspection, cleaning, and storage protocols are key to long-term cleanliness and compliance.
To keep them in good, effective condition:
- Follow proper handling procedures during gowning and removal
- Store garments in sealed, contaminant-free containers
- Launder in certified cleanroom facilities only
- Decontaminate consistently based on usage level
- Inspect for wear and damage regularly and replace as needed
One way to simplify cleanroom garment maintenance is to rent uniforms from a company that specializes in cleanroom apparel. A qualified provider will launder garments in certified facilities and deliver fresh, compliant uniforms on a regular schedule. This ensures you always have properly maintained apparel on hand while minimizing internal overhead.
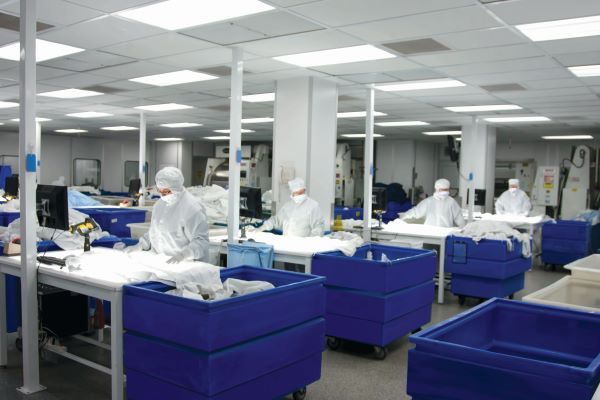
Selecting the Right Cleanroom Uniform Service
Partnering with a reputable cleanroom uniform service is imperative for maintaining a contamination-free environment. Such services should comprehensively understand cleanroom protocols and tailor their offerings accordingly.
That’s why so many facilities trust Prudential Cleanroom Services, a division of Prudential Overall Supply. Our programs are built specifically for regulated environments where cleanliness, consistency, and reliability are non-negotiable.
Addressing Cleanroom Needs
Prudential Cleanroom Services emerges as a dependable provider of cleanroom garments, apparel, and products. Our commitment to innovation ensures that our solutions align with the evolving demands of cleanroom environments.
Embodying Trustworthiness
ISO 9001:2015 certified, Prudential Cleanroom Services instills confidence through its accreditations and adherence to stringent standards. Clients can rely on our supplied uniforms and products to uphold the integrity of cleanroom environments effectively.
Certified Cleanroom Laundering
In industries where cleanliness is non-negotiable, the laundering of uniforms in a certified cleanroom environment is paramount. Prudential Cleanroom Services’ laundering processes adhere to rigorous standards, further bolstering the cleanliness of cleanroom apparel.
Get in touch with us today to learn more about how we can help you manage your cleanroom right.
📞 Call 800-767-5536
Sources:
- Little Brothers Construction, Inc. Common Causes of Cleanroom Contamination.
- Cherwell. The Weakest Link in the Cleanroom Environment? Humans.